Ultrasonic Testing (UT)
Test the thickness and integrity of your equipment with Ultrasonic Testing. UT is a safe and effective testing method that uses high-frequency sound waves to detect a material’s anomalies smoothly and efficiently.
Ultrasonic Testing and Inspection (UT)
Ultrasonic Testing (UT) is a method of non-destructive testing used to check the condition of vessels, pipelines, and production lines without causing damage. It helps find issues like erosion, corrosion, and material thickness, which can prevent costly equipment failures and downtime. Shear wave inspection, a precise ultrasonic testing technique, is commonly used for weld inspections. It involves using an ultrasonic probe with a plastic or lucite wedge to emit angled ultrasonic beams, which can detect weld discontinuities when moved. Unlike radiography, shear wave inspection can be used on various materials without thickness limitations, providing accurate measurements of defects' length and depth.
How It Works
Ultrasonic testing uses electrical charges to detect material defects. We start by setting up our equipment and emitting short ultrasonic pulse waves into the material we're testing. These waves travel through the material and bounce back to the technician, reflecting off any surface flaws like cracks. The technician then interprets the results on the 'A-Scan' presentation, pinpointing flaw locations and assessing material thickness. Unlike radiography, ultrasonic testing is versatile and can detect a wide range of defects with fewer limitations.
Discover Defects In Your Equipment:
Lack Of Fusion, Incomplete Penetration, Undercuts, Hollow Bead, Porosity and Pinholes, Tungsten or Slag Inclusion, Burn-Through or Icicles, Internal Concavity, and Cracks.
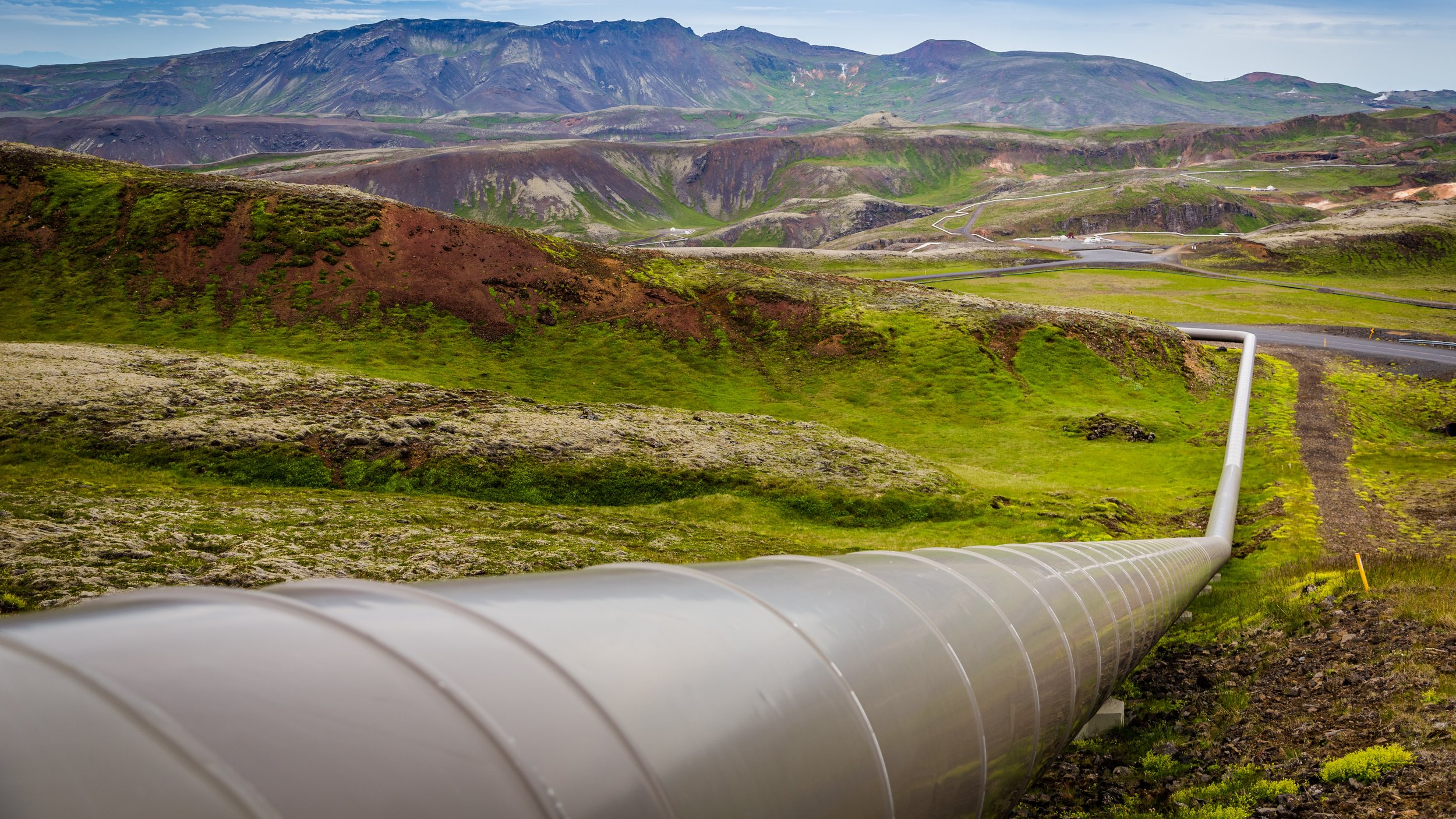
Ultrasonic Testing:
By The Industry
Due to its non-destructive nature, Ultrasonic Testing (UT) has the potential to benefit several industries. Anode NDT has years of extensive experience performing non-destructive testing for:
Oil & Gas
Construction
Forestry (Pulp & Paper)
Nuclear
Ultrasonic Testing:
Shear Wave Inspection
Anode NDT commonly uses Radiographic Testing (RT) or X-Ray to inspect the following for subsurface flaws and defects throughout Grande Prairie, Dawson Creek, Peace River, Fort St. John, and throughout northern Alberta and British Columbia:
Pressure Vessels
Industrial Facilities
Custom Fabrications and Bridges
Pipelines
Ultrasonic Testing:
Baseline Thickness Test
Well-maintained equipment guarantees superior Baseline Thickness Testing for our clients in Grande Prairie, Dawson Creek, Peace River, Fort St. John, and throughout northern Alberta and British Columbia.
We use digital ‘A-Scan’ presentation flaw detectors for our ultrasonic sets.
Devices maintain meticulous measurements (plus or minus 0.005”) and remain calibrated to either meet or exceed code requirements.
We use Integrity Plugz for safe access to industrial equipment, preventing damage to tested assets.
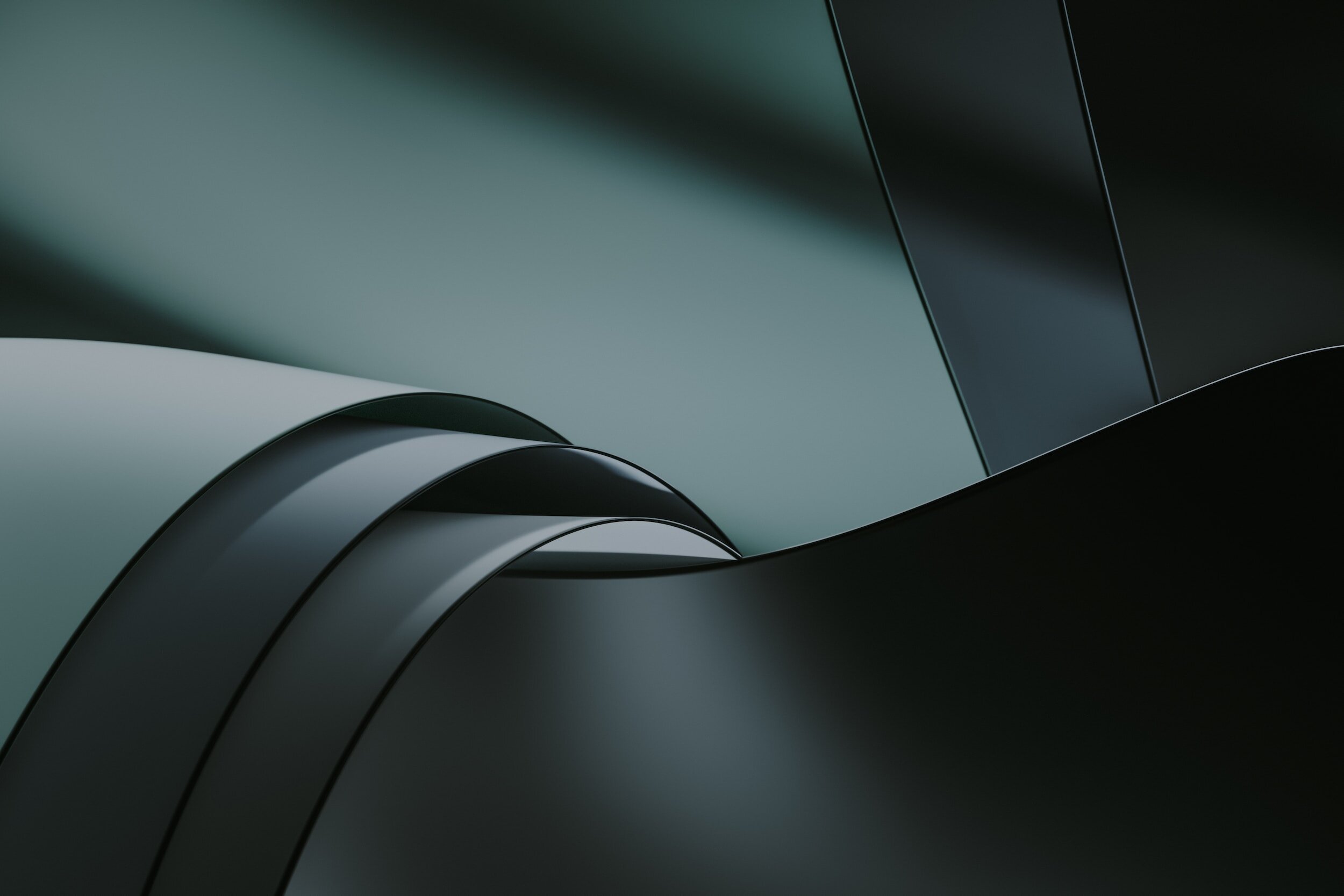
We Meet and Exceed Safety and Code Compliances
Safety is paramount to Anode NDT: both our technicians and our procedures prioritize efficiency and safe work practices.
All Anode NDT procedures are ABSA demonstrated and backed with CGSB / ASNT Level III certified support.
We proudly hold ASNT Level II certification.
Our in-house safety program is ISNetworld, ComplyWorks, Avetta, and COR compliant.